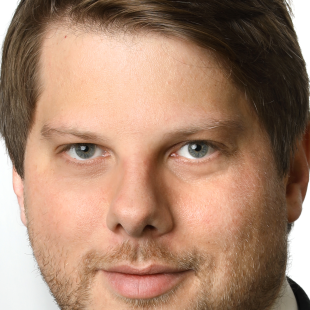
Dr.-Ing. Mathias Bobbert
Geschäftsführer -
- E-Mail:
- mathias.bobbert@lwf.uni-paderborn.de
- Telefon:
- +49 5251 60-3035
- Büroanschrift:
-
Pohlweg 47-49
33098 Paderborn - Raum:
- P1.4.12.3
- E-Mail:
- mathias.bobbert@lwf.upb.de
- Telefon:
- +49 5251 60 3035
Publikationen
Aktuelle Publikationen
C.R. Bielak, M. Böhnke, J. Friedlein, M. Bobbert, J. Mergheim, P. Steinmann, G. Meschut, in: Materials Research Proceedings, Materials Research Forum LLC, 2023.
M. Böhnke, C.R. Bielak, J. Friedlein, M. Bobbert, J. Mergheim, P. Steinmann, G. Meschut, in: Materials Research Proceedings, Materials Research Forum LLC, 2023.
M. Böhnke, C.R. Bielak, M. Bobbert, G. Meschut, in: Lecture Notes in Mechanical Engineering, Springer Nature Switzerland, Cham, 2023.
J. Friedlein, C.R. Bielak, M. Böhnke, M. Bobbert, J. Mergheim, P. Steinmann, G. Meschut, in: Materials Research Proceedings, Materials Research Forum LLC, 2023.
C.R. Bielak, M. Böhnke, M. Bobbert, G. Meschut, in: Lecture Notes in Mechanical Engineering, Springer Nature Switzerland, Cham, 2023.
Alle Publikationen anzeigen