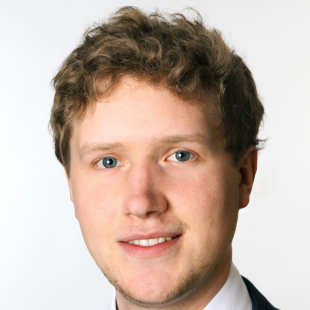
M. Sc. Fabian Kappe
Wissenschaftlicher Mitarbeiter
- E-Mail:
- fabian.kappe@lwf.uni-paderborn.de
- Telefon:
- +49 5251 60-5328
- Büroanschrift:
-
Pohlweg 47-49
33098 Paderborn - Raum:
- P1.4.10.3
- E-Mail:
- fabian.kappe@lwf.upb.de
- Telefon:
- +49 5251 60 5328
- Web:
- Homepage (Extern)
Publikationen
Aktuelle Publikationen
D. Han, F. Kappe, J. Vorderbrüggen, J. Jendrny, E. Gorr, G. Meschut, Journal of Manufacturing Processes 116 (2024) 92–108.
L. Butzhammer, F. Kappe, G. Meschut, T. Hausotte, in: Materials Research Proceedings, Materials Research Forum LLC, 2023.
S. Wituschek, F. Kappe, G. Meschut, M. Lechner, in: Materials Research Proceedings, Materials Research Forum LLC, 2023.
G. Meschut, M. Merklein, A. Brosius, D. Drummer, L. Fratini, U. Füssel, M. Gude, W. Homberg, P.A.F. Martins, M. Bobbert, M. Lechner, R. Kupfer, B. Gröger, D. Han, J. Kalich, F. Kappe, T. Kleffel, D. Köhler, C.-M. Kuball, J. Popp, D. Römisch, J. Troschitz, C. Wischer, S. Wituschek, M. Wolf, Journal of Advanced Joining Processes 5 (2022).
F. Kappe, S. Wituschek, M. Bobbert, M. Lechner, G. Meschut, Production Engineering (2022).
Alle Publikationen anzeigen