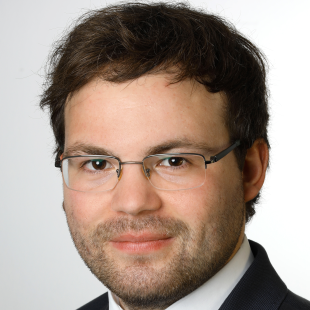
Benedikt Uhe, M.Sc.
Wissenschaftlicher Mitarbeiter
- E-Mail:
- benedikt.uhe@lwf.uni-paderborn.de
- Telefon:
- +49 5251 60-3760
- Büroanschrift:
-
Pohlweg 47-49
33098 Paderborn - Raum:
- P1.4.16
Publikationen
Aktuelle Publikationen
B. Uhe, C.-M. Kuball, M. Merklein, G. Meschut, Production Engineering (2024).
C.-M. Kuball, B. Uhe, G. Meschut, M. Merklein, Journal of Advanced Joining Processes 9 (2024) 1–13.
B. Uhe, G. Meschut, Journal of Manufacturing Processes 125 (2024) 354–363.
B. Uhe, G. Meschut, Lösungsstrategien Für Das Halbhohlstanznieten von Höchstfesten Und Ultrahöchstfesten Stählen Mit Aluminiumwerkstoffen, 2023.
B. Uhe, C.-M. Kuball, M. Merklein, G. Meschut, in: K. Mocellin, P.-O. Bouchard, Régis Bigot, T. Balan (Eds.), Proceedings of the 14th International Conference on the Technology of Plasticity - Current Trends in the Technology of Plasticity., Springer, Cham, 2023, pp. 64–71.
Alle Publikationen anzeigen