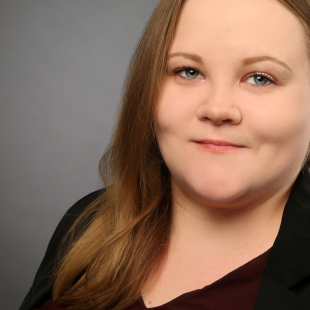
M. Sc. Annika Oesterwinter
Transregional Collaborative Research Centre 285
Member - Former
Teilprojekt C03
- E-Mail:
- ao@luf.upb.de
- Phone:
- +49 5251 60 5953
- Web:
- Homepage (Extern)
Publications
Latest Publications
Identification of Requirements for FE Modeling of an Adaptive Joining Technology Employing Friction-Spun Joint Connectors (FSJC)
A. Oesterwinter, C. Wischer, W. Homberg, Metals 12 (2022).
Comparative Analysis of Electrohydraulic and Electromagnetic Sheet Metal Forming against the Background of the Application as an Incremental Processing Technology
T. Heggemann, V. Psyk, A. Oesterwinter, M. Linnemann, V. Kräusel, W. Homberg, Metals 12 (2022).
A flow forming process model to predict workpiece properties in AISI 304L
B. Arian, A. Oesterwinter, W. Homberg, J. Rozo Vasquez, F. Walther, L. Kersting, A. Trächtler, in: 19th Int. Conference on Metal Forming 2022, 2022.
Show all publications