Willkommen im Direct Manufacturing Research Center - Academic
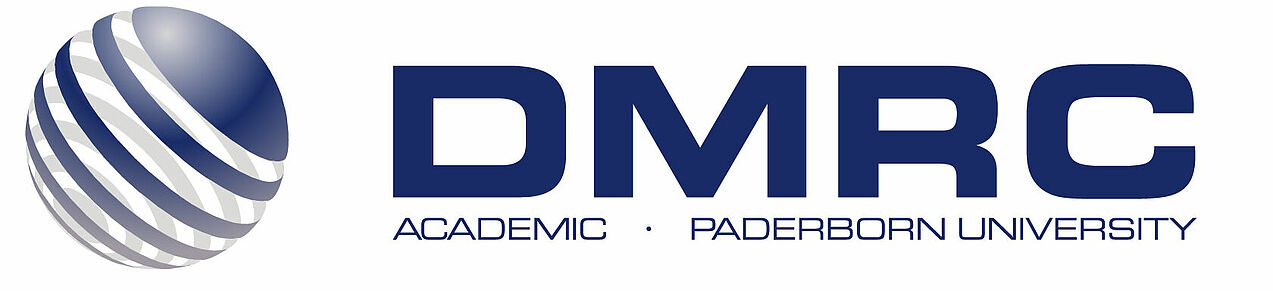
Das Direct Manufacturing Research Center (DMRC) - Acadamic, ein an der Universität Paderborn angesiedeltes Transferinstitut, forscht daran, die additive Prozesskette als robustes industrielles Produktionsverfahren zu etablieren. Hier arbeiten technologieführende Industrieunternehmen Hand in Hand mit Forschern der Universität an der Industrialisierung der additiven Fertigung. Die gesamte additive Wertschöpfungskette von der Rohstoffgewinnung über die Fertigung bis zur Anwendung wird sowohl von großen als auch von kleinen und mittelständischen Unternehmen abgedeckt. Die Struktur des DMRC ist sehr flexibel und interdisziplinär; je nach den aktuellen Forschungsthemen kann die Konstellation der am DMRC beteiligten Lehrstühle verändert werden.
Derzeit arbeiten im DMRC 11 verschiedene Lehrstühle und eine großen Anzahl von wissenschaftlichen Mitarbeitern zusammen.
Je nach Fragestellung und Zeithorizont finanzieren die Industriepartner des DMRC oder öffentliche Förderorganisationen Forschungsprojekte, die dann an der Universität Paderborn durchgeführt werden. Die im DMRC-Konsortium gemeinsam finanzierten Projekte werden dabei von den Industriepartnern gesteuert und kontrolliert. So können alle Partner den größtmöglichen Nutzen im Hinblick auf die Industrialisierung der DMRC-Forschungsergebnisse erzielen.
Mitarbeitende
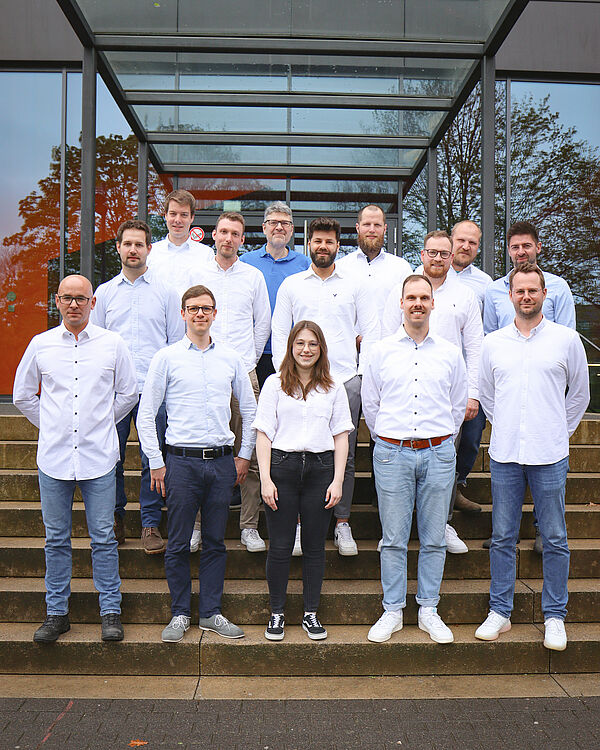
Am DMRC sind zur Zeit
3 Direktoren,
11 Vorstandsmitglieder*innen,
14 wissenschaftliche Mitarbeitende
und 1 technischer Mitarbeiter
beschäftigt.
Stellenausschreibungen
Gestalten Sie mit uns die Zukunft!
Das Direct Manufacturing Research Center (DMRC) ist eine zentrale wissenschaftliche Einrichtung der Universität Paderborn, welche die Aktivitäten von mehr als 12 Lehrstühlen in 3 Fakultäten im Bereich der additiven Fertigung bündelt. Dazu gehört auch die enge Kooperation mit einem Konsortium von ca. 25 internationalen Industriepartnern zur Durchführung anwendungsnaher Forschung in diesem Bereich.
Wir suchen zum nächstmöglichen Zeitpunkt eine*n wissenschaftliche*r Mitarbeiter*in (w/m/d) als Geschäftsführung.
Ausführliche Stellenbeschreibung: PDF
Ansprechpartner: Prof. Dr.-Ing. Hans-Joachim Schmid
Gestalten Sie mit uns die Zukunft!
In der Fakultät für Maschinenbau an dem Lehrstuhl für Partikelverfahrenstechnik (PVT) in Kooperation mit dem Direct Manufacturing Research Center (DMRC) ist zum nächstmöglichen Zeitpunkt eine Stelle als wissenschaftliche*r Mitarbeiter*in (w/m/d) zu besetzen.
Ausführliche Stellenbeschreibung: PDF
Ansprechpartner: Herr Steffen Jesinghausen
Adresse
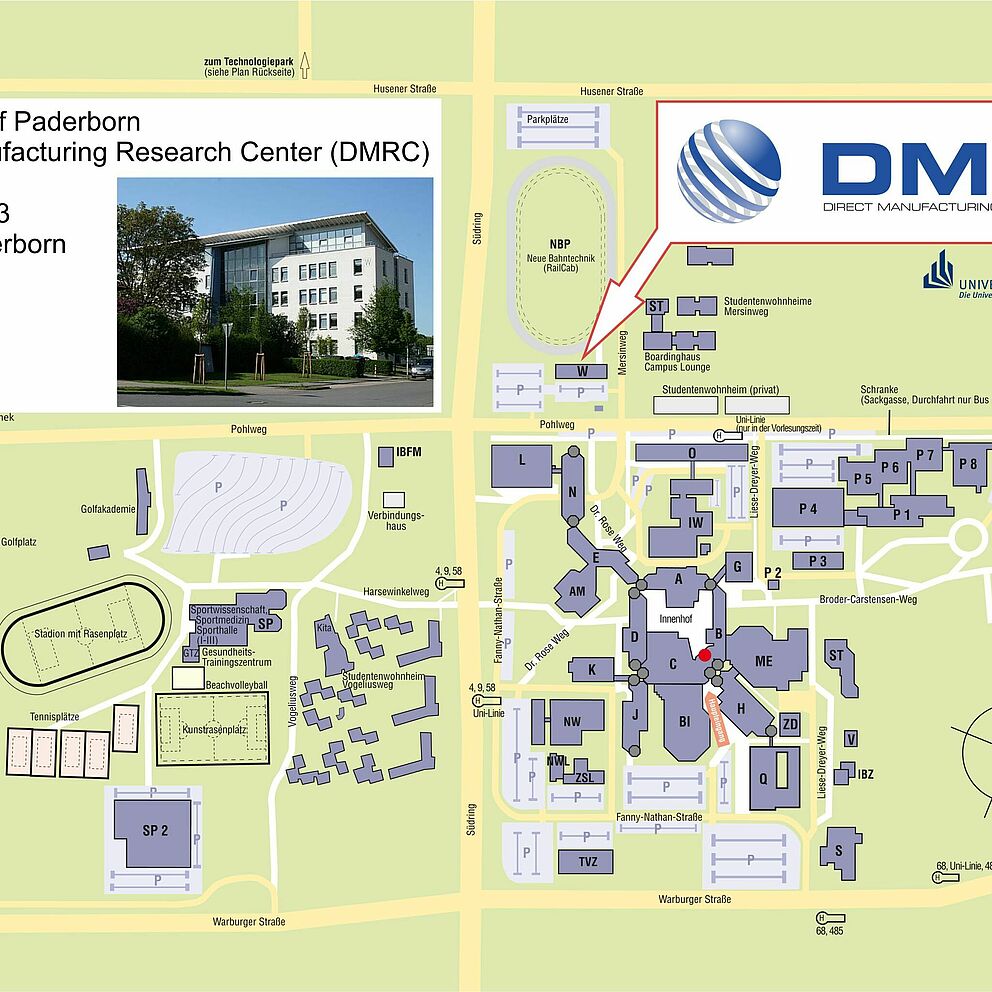
Anfahrt
Direct Manufacturing Research Center (DMRC) – Academic
Mersinweg 3
33100 Paderborn